Supply Chain Magazine a réalisé en juin 2017 l’interview de l’équipe projet WMS Infor de l’industriel MP Hygiène. En voici quelques extraits :
MP HYGIENE fédère ses équipes autour de son projet WMS
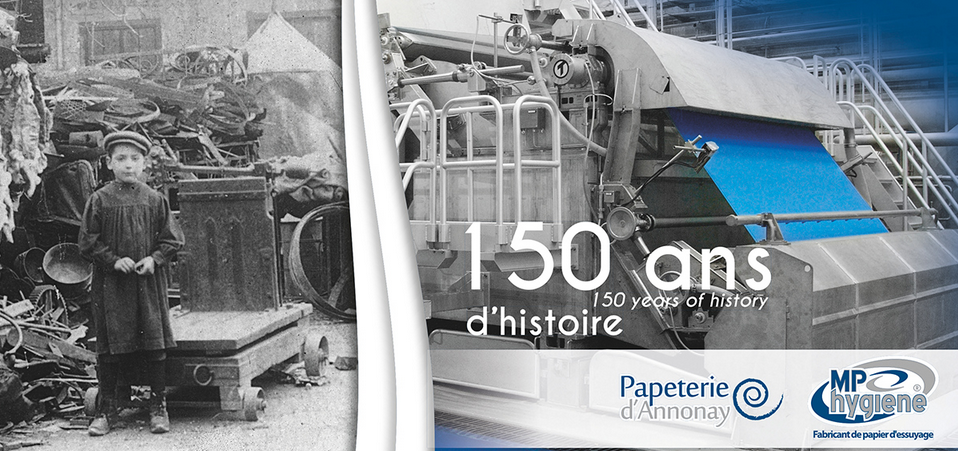
MP Hygiene, fabricant ardéchois de papier d’essuyage a fait appel à SNS ALOER pour le guider dans la mise en œuvre d’Infor WMS sur ses 4 sites d’entreposage et de production. 15 jours de rude mise en route menée pendant la migration de l’ERP ont contribué à rapprocher les équipes logistiques. Surmontant ensemble la charge de travail, elles ont su tirer profit des efforts fournis pour gagner en fiabilité et en performance.
Spécialisée dans la fabrication de papier d’essuyage labellisé Origine France Garantie, MP Hygiène est une société familiale. Dirigée depuis 1997 par Marc Miribel, son PDG, elle compte 4 sites (dont 3 de production /stockage et 1 de stockage) sur 51.000 m² et 21 lignes de production. Chacun des sites peut préparer des commandes, qui peuvent être regroupées selon diverses méthodes adaptées aux clients. Ayant réalisé un CA de 67 M€ en 2015, elle emploie environ 180 personnes.
Une prospection opportune et un bon feeling
Pour faire face à la croissance de ses activités de 5 à 15% par an, mais surtout de ses stocks de matières premières et de produits finis, MP Hygiène a voulu mettre en place un WMS - Warehouse Management System - afin de progresser en adoptant de bonnes pratiques rigoureuses.
« Il y a 2 ans, nous avons décidé d’améliorer la qualité, le service et la réactivité de la Supply Chain, qui était le secteur où l’on avait le moins investi, comparé à l’ERP de production. Nous avions le projet d’abandonner le papier / crayon depuis plusieurs années, mais conscients que cela prendrait beaucoup de temps, nous l’avions repoussé », reconnaît Émeric Guillermain, Directeur Supply Chain de MP Hygiène.
Décision est alors prise par le PDG de se lancer. N’ayant pas l’expérience de tels projets, l’idée est de trouver des consultants pouvant apporter leur expertise. C’est à ce moment opportun que MP Hygiène démarche ALOER et qu’après diverses consultations (un cabinet recommandé par un transporteur, d’autres régionaux recensés via des magazines), le fabricant lui confie son projet WMS.
« SNS ALOER est venu avec des consultants spécialistes de WMS. On voyait tout de suite qu’ils savaient de quoi ils parlaient. Ils avaient de solides références. Le feeling a beaucoup joué dans le choix de l’intégrateur », pointe le Directeur Supply Chain.
Infor WMS l’emporte avec SNS ALOER comme intégrateur
L’équipe de projet de MP Hygiène, guidée par SNS ALOER, établit le cahier des charges de juin à décembre 2015.
« L’équipe de projet de MP Hygiène se composait d’opérationnels pour qui assurer la continuité d’activité était primordiale et peu rompus à l’exercice de description écrite des processus. Les gens de SNS ALOER, plutôt de formation universitaire informatique, trilingues et ayant une capacité à entrer très vite dans la culture du projet, étaient complémentaires » analyse Étienne GEORGES, dirigeant ALOER.
10 éditeurs de logiciels WMS sont consultés
Parmi les éditeurs de logiciels WMS consultés, seuls 5 répondent :
- Acteos,
- BK Systèmes,
- Hardis,
- Infor,
- et Sage.
À l’issue de l’analyse des dossiers reçus et des démonstrations, le système de notation fait ressortir de l’appel d’offres qu’Infor WMS est le meilleur compromis …
« À l’origine, nous voulions des Français ! Si la solution d’Infor était plus chère, moins sexy que les autres mais techniquement aussi bonne voire meilleure, elle disposait aussi nativement d’un module de gestion des entrées/sorties de matières premières s’appuyant sur des gammes et des nomenclatures permettant d’optimiser les approvisionnements en les amenant au fur et à mesure de leur consommation » explique Émeric Guillermain.
« C’est une fonction couramment utilisée en production aux États-Unis et au Moyen Orient » ajoute Wael Mabsout, Senior Manager SNS et Chef du projet.
Un démarrage houleux mais fédérateur
Le 27 mars 2017, l’équipe projet appuie sur le bouton…
« La 1ère semaine a été la pire de ma vie, ainsi que pour mes équipes. Et la seconde, nous sommes passés de « on va tous se suicider » à « c’est génial !» s’exclame Émeric Guillermain.
Malgré l’attention apportée à la conduite du changement et à la formation, des bugs au démarrage consécutifs à des situations non ou mal envisagées en amont sabrent le moral des équipes. Certains s’accrochent tandis que d’autres décrochent et rejettent la solution.
« Heureusement que les consultants de SNS ALOER étaient là. Ils n’ont pas vu leur famille pendant 3 semaines et se sont comportés non comme des fournisseurs mais comme des membres à part entière de notre équipe. Ils s’appropriaient les problèmes, et traduisaient en code les solutions techniques et de process. C’était fort …, se souvient le Directeur Supply Chain. Il nous a fallu 15 jours pour être autonomes. Les 10 super-utilisateurs ont aidé les 30 autres utilisateurs afin que tout le monde apprenne à se servir de la nouvelle solution. Le fait d’être tous dans la même galère a ressoudé les équipes. Ils prenaient leur café ou leur pause cigarette ensemble. Les consultants ont eu des surnoms…».
De nombreux gains à mesurer
Les bienfaits de la nouvelle solution se sont fait sentir dès la 2e semaine.
« Lorsque des erreurs humaines étaient commises, nous savions en 2 secondes par qui, comment … pour corriger au plus vite. A présent, retracer un produit ou une fabrication se fait rapidement, ce qui n’était pas possible avant. Nous préparons aussi plus vite les palettes complètes » liste Émeric Guillermain.
Il estime pouvoir encore faire des gains au niveau du picking, de la gestion A, B, C plus précise.
« Je pense que nous devrions économiser 25% de charges d’expédition et que nous devrions gagner en taux de productivité sur la préparation de commandes. L’inventaire de fin d’année, qui mobilisait les équipes 1 week-end 14h/j, devrait aussi être plus facile en raison de la précision du suivi » estime-t-il.
La prochaine étape de ce projet, qui a requis 1 M€ d’investissement (installations et matériels – PDA et terminaux, logiciels, service…) va être de « corriger les bugs restants » et de faire évoluer la gestion des caristes.
« Nous voulons optimiser les chemins de préparation par rapport au classement A, B, C, nous connecter au transport, gérer des indicateurs pour affecter au mieux les dossiers aux caristes … » envisage le Directeur Supply Chain.
Le projet WMS : Une réussite collégiale
« Si c’était à refaire, je ferais plus attention à la conduite du changement. Il faut vraiment avoir les bons gars en interne et en externe. Il faut veiller aussi à ne pas prendre de risques inutiles. Comme la mésaventure que nous avons eue avec des étiquettes en jouant sur les prix qui aurait pu faire capoter le projet. Ma femme a vécu 2 ans difficiles. Ce ne sont pas des projets à prendre à la légère, surtout quand on sait que 30% des projets au global seulement arrivent au bout ! Il est aussi important d’avoir la confiance de son patron…», analyse Émeric Guillermain.
Il souligne également le rôle joué par ALOER, en tant qu’Assistant à Maîtrise d’ouvrage : « L’AMOA nous ont aidés à recadrer les consultants et mes gars, par rapport à ce qui avait été dit. Elle a su repousser la date de démarrage du projet lorsqu’elle a estimé que nous n’étions pas prêts. Nous, nous aurions foncé tête baissée, n’ayant pas la culture du cahier des charges ».
Au bout du compte, le projet est un succès
Le chiffre d’affaires réalisé en début d’année est aussi bon, voire meilleur. Le budget a été globalement respecté. Et les perturbations vécues en interne ont été transparentes pour les clients : aucuns retards dus au WMS.
« Sur ce projet, la volonté de bien faire est venue de tout le monde. C’est positif de travailler avec des gens qui ont un esprit entrepreneur. Par contre, même si on teste, cadre et exécute chaque étape, il y a une nécessaire étape d’apprentissage. L’appropriation de l’outil est une étape que seules les équipes utilisatrices peuvent franchir », observe Étienne Georges.
Il ajoute néanmoins avec satisfaction : « MP Hygiène va bien au-delà de ce qu’il attendait en termes de R.O.I. ».
Le fabricant envisage de construire 2 nouveaux entrepôts dans le cadre de son développement international. Gageons qu’avec le savoir-faire acquis sur ce projet, la mise en œuvre du WMS devrait se passer facilement …
Contactez-nous et exposez-nous votre projet d’amélioration d’entrepôt
tel:+33478773690
Partager la publication « Le projet WMS de MP HYGIENE – Retour d’expérience sur Supply Chain Magazine »