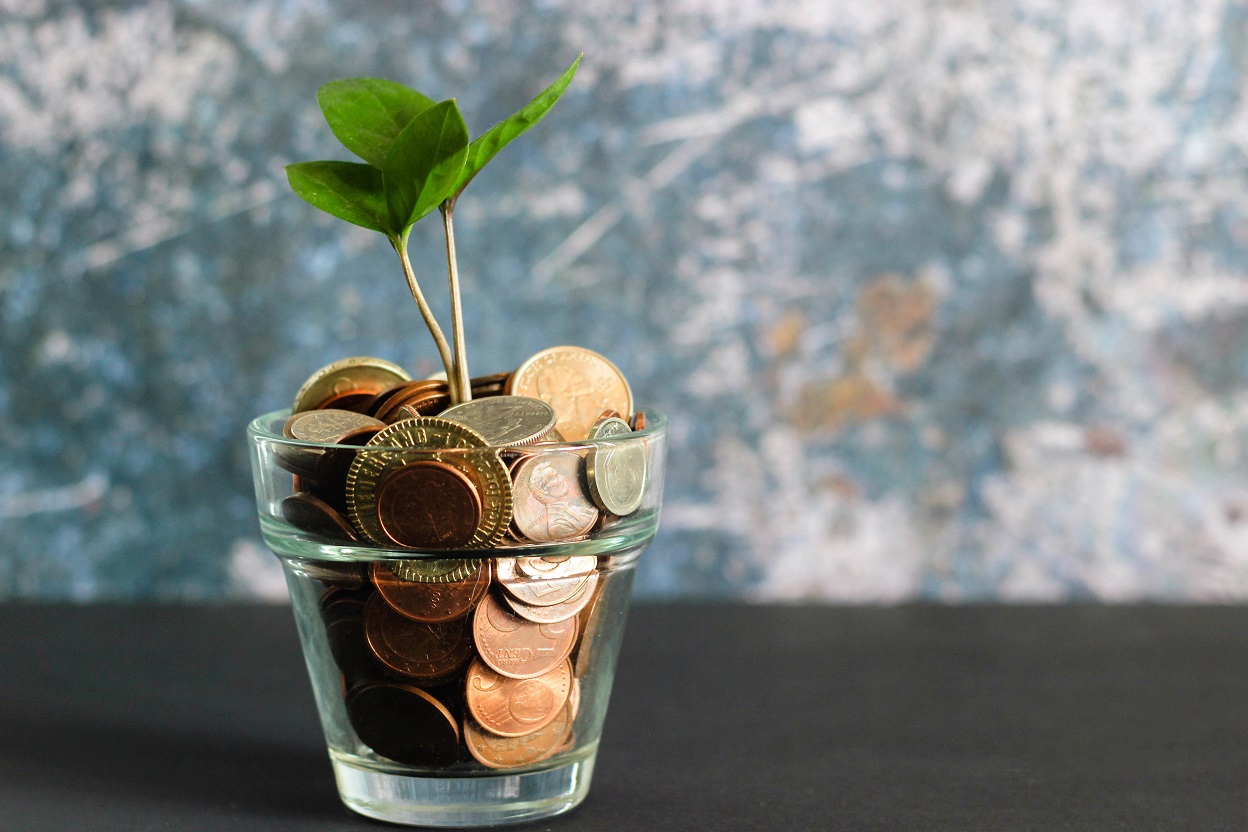
Inventory Holding Cost : no inventory, no costs?
If you have no inventory, you have no costs. Conversely, the more you increase your inventory, the more your carrying cost will increase.
As you can see, inventory carrying costs are the costs associated with storing and maintaining inventory for a certain period of time.
Generally, they are defined as a percentage of the value of the inventory and they vary greatly depending on the field of activity of the companies. It is commonly accepted that storage costs represent up to 25% of the value of the available stock.
Stock definition
Stock is any item or product held by a company, which is the result of the difference between the inflow of items and their outflow.
The output flow corresponds to the consumption of customers for finished products and the consumption by production for raw materials. The orders and/or forecasts will define the stock requirements to meet the customer’s demand in time, quality and quantity. This flow corresponds to the orders is not “controllable” by the company. It can fluctuate significantly from month to month. The input flow corresponds to the orders placed by the procurement and inventory management teams. This is the only flow that any company can really control.
The company therefore has only one lever to regulate its stock. Indeed, if it controls the incoming flow correctly, it avoids the risk of creating either overstock or stock-outs.
About the need to have a stock ?
The existence of the stock could be summarized as follows: the fact that the company wants to satisfy the customer demand.
Thus, the stock allows the company to continue to satisfy customer demand even if there is a gap between the incoming flow (supplies) and the outgoing flow (customer orders). Indeed, it can often be seen that the time to obtain materials and production is greater than the time to process the customer’s order. But that’s not the only reason why a company builds up inventory.
Stocks and functions
- Regulation: stocks allow the smoothing of irregularities in supply and/or production, reduce the risk of stock-outs and help maintain a continuous activity
- Logistics: the stocks allow to keep the articles close to their place of consumption. They significantly reduce waiting times
- Economic function : when the supplier grants important discounts for large quantity purchases, storage can be useful. In the same way, in order to optimize supplies, the constitution of a stock is generally an appropriate solution
- Anticipation: storage allows to manage price increases of materials or products bought or sold. These are seasonal stocks
- The technique: the stock can be linked to a process constraint before the consumption of the articles. This is the case for the drying of wood, the ripening of fruits and vegetables, the fermentation of wines…
The problem of overstock is primarily financial. All inventory costs the company.
Inventory Holding Cost
Most logisticians and business leaders agree that inventory costs, but few know the details of their own storage costs.
It is estimated that the inventory costs between 15 and 35% of its value per year. This percentage, called the “Possession Rate” is a quick way to give an overview of the financial burden of an inventory.
In theory this estimate is sufficient, but in practice this possession rate cannot be used alone. In effect, it makes the cost vary linearly with the quantity of items in stock. However, the cost of ownership can vary in steps and not linearly.
For example, if you need to build a new warehouse or bring in a new contractor (3PL) to increase your storage capacity, you will have to make an investment that will affect your overall inventory costs, see below the storage costs.
This cost is composed of 3 elements
- Financial costs: owning stock means advancing money until the finished product is sold. In addition, some companies borrow to finance their inventory, which results in additional costs
- Warehousing costs”: this item covers all costs related to storage. We will find the salaries of the storekeepers, the carts maintenance costs, the building or insurance cost, the information system cost …
- “Depreciation costs”: these costs represent expenses related to changes in inventory over a period.
It is important to monitor this element as well as the logistics performance indicators because they are a good way to evaluate the impact of the inventory management policy on the company’s finances.
The calculation of inventory carrying costs on Christian Hohmann’s blog
« Back to Glossary Index